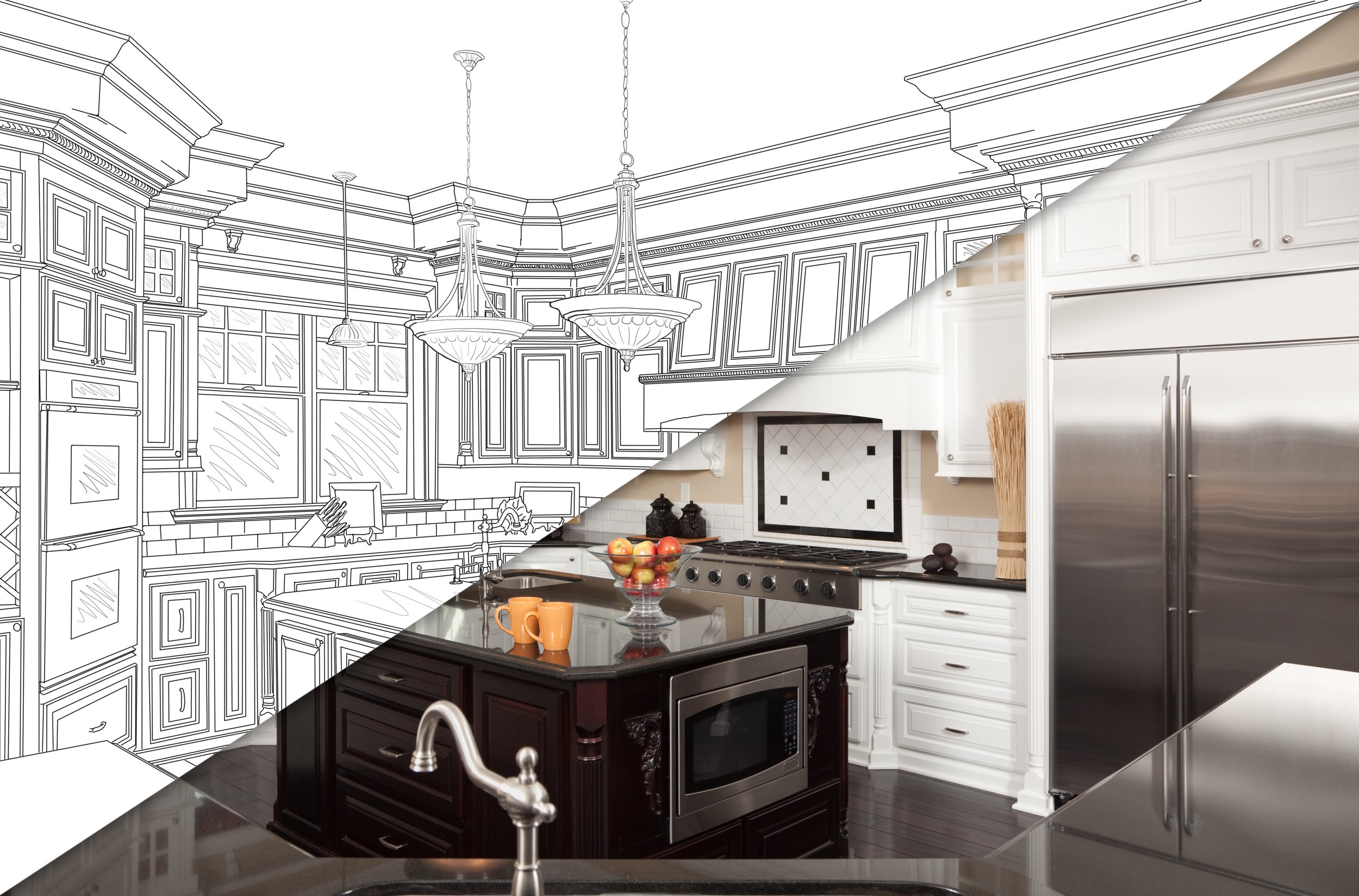
Dedicated to Exceptional
Craftsmanship
Founded in 2010, IronHorse Designs is a business dedicated to the art of Finish Carpentry & unique Custom Furniture. From grand statement pieces in a room to one of a kind heirloom furniture, we approach every project as a unique opportunity to create something beautiful built to last. Applying generations of woodworking & finish carpentry techniques to modern aesthetics, we are committed to shaping the future of woodworking and carpentry!
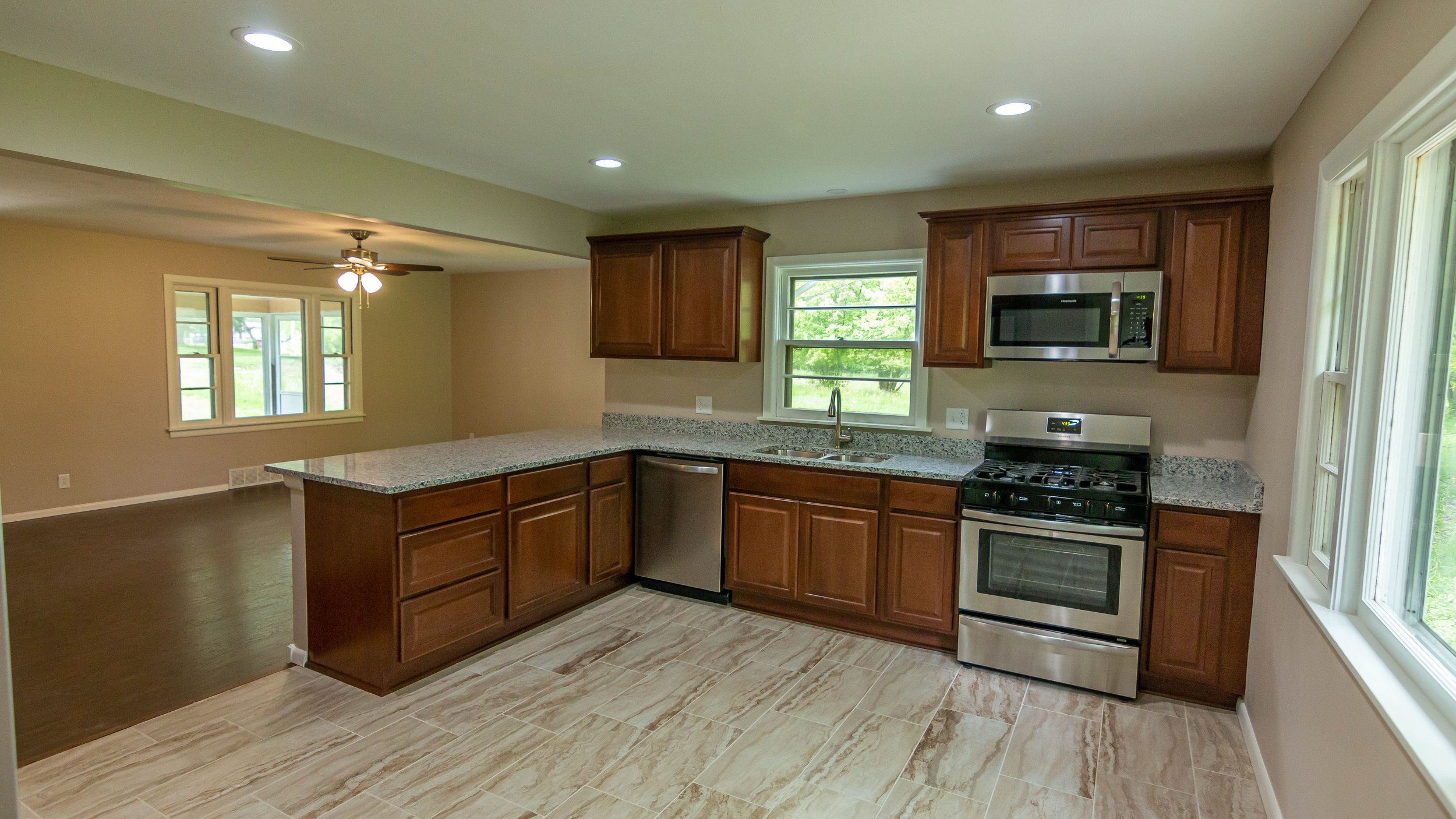
“My mission is to provide one of a kind custom hardwood furniture and millwork that is built to last beyond a lifetime. Every single piece is built and installed with care, integrity, and pride to ensure unmatched quality you will only find here. I do not consider myself a cookie cutter craftsman, but rather someone who can do a lot of different things that are considered quite rare!”
— Daron Kettler
Learn more about our process below…..
Finish Carpentry & Millwork
-
This can be in-person, phone, or a video conference call to discuss your project. We’ll discuss what phase you are in of the project, and other details to help us understand your needs.. Such as what type of trim work or millwork is specified, doors, cabinets, etc. and overall timeline.
-
Once we’ve discussed your project in more detail it is time to give you an idea on the cost. We will review the plans (and elevations if you have them) to perform a take off of material and/or labor to complete the work. Depending on the stage of your project this may require a site walk if construction has already begun. If you are at the beginning stages and need a budgetary number we can help provide that as long as we know. Then we will perform a site walk prior to rough in of electrical, HVAC, and plumbing to finalize the pricing.
-
We are unique here at IHD in that we prefer to review the proposal with the client either in person or video chat. There is a full walk through of the scope, assumptions, and clarifications on the pricing. This is so that you, the client, knows exactly what you will be getting if you choose to go with us!
-
If we are awarded the job then let’s get it on our calendar so that we are available when you need us. We will provided a suggested schedule for site visits at given milestones to ensure that the end product is what you are expecting, perfection!
-
Yes, it’s unusual for the Finish Carpenter to show up once rough-in is complete but it is a necessary evil! We walk the sites to identify and mark out electrical & water lines, backing required, door plumbness & square, and ensure there are no changes at this stage to the plan. We document everything and take very detailed 360 degree photos and inwall photo’s for later when everything is covered up. This ensures that doors are installed perfectly, trim is nice and tightly mitered, and that there is adequate backing in the walls for any additional millwork required.
-
We will coordinate with you and/or the PM on delivery of the trim and millwork to the project site. Typically this 1-2 weeks ahead of when we will be starting the work. Material must be stored inside the home so that the wood has time to adjust to the humidity and climate inside. We will provide trim racks the day prior to the delivery for everything to be placed and staged on.
-
Finally the day has come! We will begin to install doors, cabinets, and then finally any trim and millwork. At this point it is assumed that material has been delivered and has had a chance to properly acclimate to its environment inside the house.
Learn about our Furniture build process...
-
Let’s meet…..information on a website is great but I still prefer a good old fashion discussion about your piece.
In a culture overrun by mass-production, a one-of-a-kind handmade good is rare. Finding someone who is skilled in Finish Carpentry, even rarer! I pride myself on making long lasting heirloom quality furniture. If you are looking for cheaply constructed furniture, I am not a good fit for you. I take pride in my work and the relationships I create as a result with our clients.
Everything I make is from scratch with every detail agonized over. I exclusively use solid hardwoods for everything – and that’s really what you want in furniture. The big box stores are notorious for gluing a very thin (1/32-inch) piece of hardwood to a very cheap and lightweight type of plywood. Not the case here. If you order a table in Hickory it will be Hickory through and through, which means it is heavy, sturdy, and durable enough to take on the tests of time, kids, applesauce, dinner parties, and homework. I currently offer several wood species including Alder, White Oak, Maple, Cherry, Hickory, and Walnut. Exotic woods are also available upon request.
So there is a bit of a wait time depending on the project. From the day you book an order to the day it’s ready for delivery/pickup, you are looking on average of about 12 weeks. And, of course, you are always welcome to check in with me on the status and timing of your order.
-
Great furniture starts with great lumber. I take the time to sort through multiple pieces of hardwood to select the perfect board for each piece. I have even been known to take the clients with me, virtually and in person, to pick their own slabs for large pieces. Even let them mill their own trees from their property when the opportunity arises!
-
Joinery and understanding the attributes of different species of wood are crucial to creating stability and longevity of our furniture. In an industry that relies on laminated tops and cheap veneers, I am dedicated to raising the bar on quality and standards!
I am a life long student of the craft and constantly learning to develop my skills. My mission is to shape the future of woodworking and raise the bar on quality within the industry.
You will not be disappointed in my work!
-
Large operations and companies rely on industrial machines to handle their sanding. Even the well known high-end furniture stores use large machines because of production quotas and demands. Not me!
Every square inch of each piece that comes out of my shop is sanded by hand. Not only sanded, but constantly inspected to make sure that the wood is sanded correctly. As much as sanding is the least favorite part of the process it is the most crucial. I know there’s a big difference between a piece of hardwood sanded by a machine and one sanded by a craftsman who cares.
I care so I sand!
-
When it comes to staining furniture, I use a slower, more intricate skill set of staining pieces by hand. I take additional steps in the process that others do not take because of time. Again, I do not take short cuts and know you will see the difference yourself. There is an art to putting color to wood; it’s a skill I am continually improving and proud to exhibit!
-
After eight build stages and eight tedious inspections, the furniture finally reaches the finishing stage. At this stage I apply the best finish based on the intended purpose of the piece. This includes either three coats of a high-end matte finish, wax, water-based lacquer, or a number of other finishes. I have invested the necessary time and skills in order to provide you a finish that is designed to stand the test of time.
-
Finally the time has come for delivery day. I will hand deliver your furniture assembled and ready to be used if local. The craftsman who helped design and build your piece will be the one that also delivers it. It is a matter of pride and satisfaction in seeing my clients when they receive their piece.
All clients will receive a care package for their piece and instructions on how to maintain their furniture so that it will retain the original finish it had at my shop!
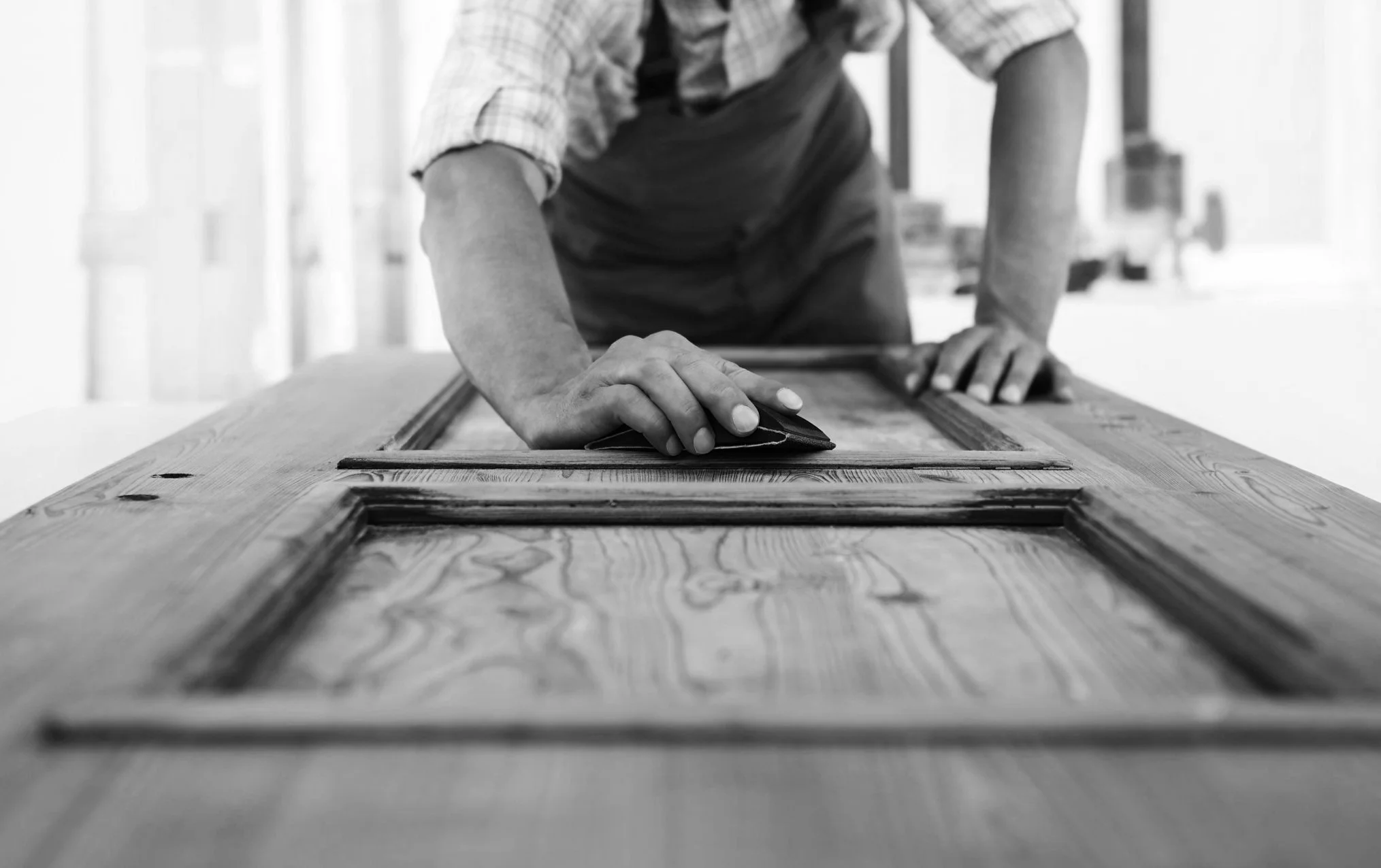
Book a Free Consultation
We would love to meet you and walk you through every step of our process.